When you’re hundreds — even thousands — of meters underground, safety isn’t something you take lightly. Shafting, whether for men and material, can be a fickle environment. But the systems spinning shafts today are light-years beyond that.
We’re reaping it in the form of smarter replacement shafts in shaft technologies, tougher materials and tighter monitoring — all coming together to help things run smoothly and to keep people safe. These are not merely marginal adjustments.
They’re changes you experience every shift, from reduced breakdowns, to improved response times. If you’ve ever taken an old lift and a new one back-to-back, you already understand the difference.
Smart Monitoring Systems
Today there is a huge amount of more sensors on shaft safety. These small guys sense motion, pressure, vibration or even gas leaks before things go off the rails. You no longer have to depend solely on someone’s gut or periodic exploratory digs.
The moment something’s awry, the system sends an alert. This reduces time for a response drastically. You can shut things down or address a problem before it proliferates. Further, those sensors feed into dashboards that log long-term trends.
Perhaps you find wearing the shaft guide before it breaks. Or perhaps you see subtle signs of instability building over time. In any case, being data-driven keeps you in the driver’s seat.
Stronger, Safer Materials
Steel still exists but is tougher and more malleable than the old kind. And that’s just for starters. Carbon fiber reinforcements, high impact polymers and wear resistant coatings are some of the shaft replacements in shaft technologies making their way into shaft technology.
These materials last longer and can withstand more abuse than other northerly-dense options. That translates to fewer part and system replacements, less downtime, and a smaller probability of something going wrong in the middle of a procedure.
Some are even experimenting with so-called self-healing coatings — materials that can seal tiny cracks by themselves. That may sound like science fiction, but it’s not. If you’ve ever had to manage a snapped cable or damaged liner mid-shift, you’ll know why that’s important.
Improved Shaft Designs
Old shafts had their limits. Right angles, not enough ventilation, no margin for error. Now designs emphasize not only efficiency, but also safety. You’ll find multiple access points, emergency ladders, wider venting channels, better lighting systems.
Engineers are designing escape routes from the outset, not as an afterthought. And loading systems are getting wiser, too. Ore skips and cages don’t just drop and lift anymore.
They are turning their speed up and down based on load, vibration and braking feedback. Even the rare scare when the lift jolts or clangs have been rare; it’s vanishing. Rail is smoother, and more importantly, more predictable.
Automated Safety Protocols
The old manual checklists are still used, but many mines employ automated safety routines. Doors do not open until a cage is properly locked. Automatic brakes kick in if speeds accelerate too quickly.
These automated scripts eliminate human error. You’re not counting on someone to remember each step under pressure.” Instead, the system keeps a few details consistent and finds if anything is out of the ordinary.
That doesn’t entail eliminating people from the process altogether — but it does mean once something goes wrong, your Hail Mary’s are stronger and come faster.
A Real-Time Feedback In Training
One of the biggest shifts? Training doesn’t end when you’re out of sight. Real-time data from shafts is now being employed in training workers more effectively. See, someone’s riding a cage too much, at too fast a speed.
That data shows up, and managers can coach them before it gets to a safety issue.” In simulators, the actual conditions of the shaft are employed to instruct on emergency procedures. Instead of hoping for the best in the event of a breakdown, workers rehearse with scenarios drawn from real data.
That makes reactions more severe and decisions quicker. It also builds confidence. When you have a sense of what to expect and how to act, the anxiety recedes — and that’s a big win.
Conclusion
The shaft systems of today are not just transporting people and ore — they are transporting responsibility. And the tech now supporting them is stepping up in ways that count.
From early warnings to sturdier buildings, smarter designs to sharper training, safety isn’t left to chance. It’s woven into the hardware, the equipment and now, the very routines of life.
You can sense it when the elevator slides without that uncomfortable lurch. You see it when inspections find nothing because the system had already identified it days before. This is how you learn things are doing fine.
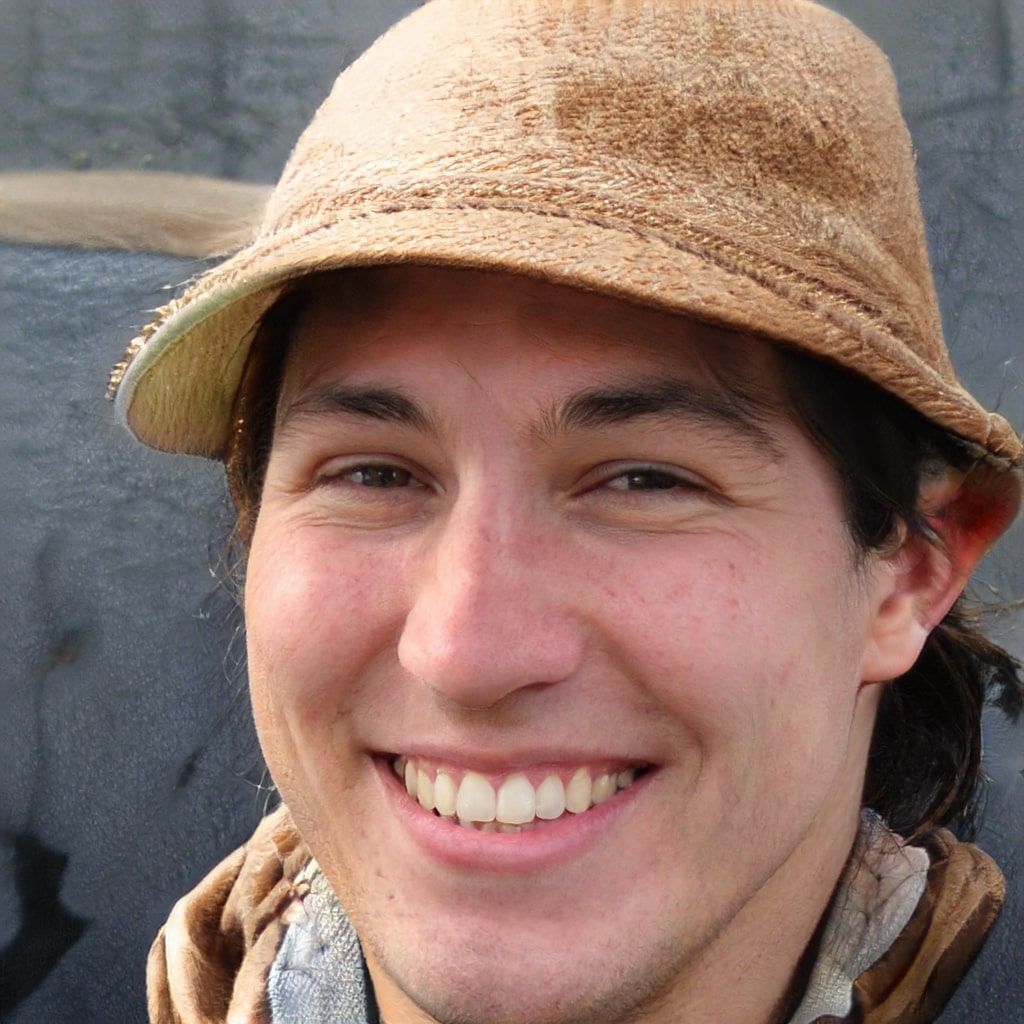